Aluminum Die Casting
ForceBeyond provides superior quality aluminum die casting parts and components for a wide range of industries including automotive, food dairy, machinery, medical, plumbing, watering, mining, petrochemical, electrical, energy, aerospace, submarine and others.
Aluminum die casting is a great choice for manufacturing parts with the highly valued combination of light weight and superior strength at a high rate. With die casting machines ranging from 180 up to 2,000 metric tons and CNC machine centers, we can produce aluminum die casting parts from a few grams to more than 40 pounds with superior quality ready for assembly. For aluminum die casting parts with requirements of esthetical, functional, or protective coatings, we also offer a broad range of surface finishing including powder coating, e-coating, shot blasting, chrome plating, and bright finish.
What Is Aluminum Die Casting?
Aluminum die casting is a manufacturing process for producing accurately dimensioned, sharply defined, smooth or textured-surface aluminum parts through the use of reusable molds, called dies. The aluminum die casting process involves the use of a furnace, aluminum alloy, die casting machine, and die. Dies that usually constructed with long-lasting, quality steel have at least two sections to permit removal of castings.
How are Aluminum Die Castings Made?
The aluminum casting dies that are created using hardened tool steel must be made in at least two sections so that castings can be removed. The aluminum die casting process is capable of producing tens of thousands of aluminum castings in quick succession. The dies are firmly mounted in the die casting machine. The fixed half die is stationary. The other one, injector die half, is movable. Aluminum casting dies can be simple or complicated, with movable slides, cores or other parts, depending on the complexity of the casting. To begin the die casting process, the two die halves are clamped together by casting machine. High temperature liquid aluminum alloy is injected into the die cavity and rapidly solidified. Then the movable die half is opened and the aluminum casting is ejected.
To date, the complete cycle of aluminum die casting has been the fastest cycle to produce precision aluminum parts. This is in stark contrast to sand casting, which requires new sand molds for each casting. Although the permanent mold process uses iron or steel molds instead of sand, it is much slower and less precise than aluminum die castings.
Watch the video of our aluminum die casting facility to learn how aluminum die castings are made. Video also available on youtube.com.
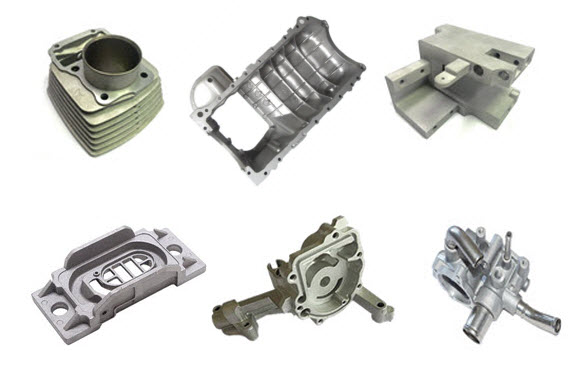
Advantages of Aluminum Die Casting
- Simple or complex shapes
- Thin wall thickness
- Light weight
- High rates of production
- Corrosion resistance
- Monolithic – combine multiple functions in one
- Efficient and economical alternative to other processes
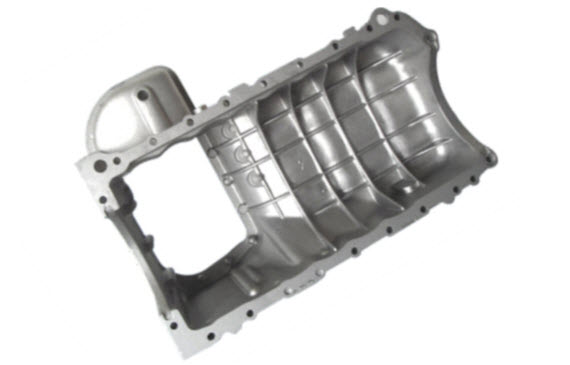
Aluminum Die Casting Material Information
Material | Tensile Strength (Mpa) | Thermal Conductivity (W/mK) | Features |
---|---|---|---|
Aluminum A380 | 325 | 96 |
|
Aluminum A360 | 317 | 113 |
|
Aluminum 413 | 295 | 121 |
|
Aluminum 383 | 310 | 96 |
|
Aluminum B390 | 317 | 134 |
|
Aluminum A413 | 290 | 121 |
|
Secondary Operations of Aluminum Die Casting We Offer
- High precision CNC machining, milling, drilling, tapping, e-coating, anodizing
- Painting, sanding, shot blasting, powder coating, chrome plating
Sources
- American Foundry Society. “Metal Casting”
- Wikipedia. “Investment Casting“, “Sand Casting“
- efunda. “Sand Casting“
- The Investment Casting Institute. “What is Investment Casting?“
- The Library of Manufacturing. “Investment Casting“
- Forging Industry Association “Forging Industry“
Our Internal Resources for Die Casting, Investment casting, Forging and Sand Casting
- Die Casting
- Aluminum Die Casting
- Zinc Die Casting
- A356 Aluminum Casting with T6 Heat Treatment
- Magnesium Die Casting
- Investment Casting
- Stainless Steel Casting
- Duplex Stainless Steel Casting
- Super Duplex Stainless Steel Casting
- Titanium Casting
- Carbon & Low Alloy Casting
- Forging
- Cold Forging
- Hot Forging
- ECO BRASS C69300 Brass Forging
- Sand Casting (Aluminum Sand Casting, Ductile Iron Sand Casting, Gray Iron Sand Casting)
- Specialty Fittings and Fasteners
- Precision CNC Machining and Secondary Operations