Turbocharger Shaft Wheel
A turbocharger shaft wheel, also known as a compressor wheel or impeller, is a key component of a turbocharger. Turbochargers are commonly used in internal combustion engines, particularly in automotive engines, to increase the efficiency and power output by compressing the air entering the engine.
The turbocharger shaft wheel is part of the compressor side of the turbocharger. It is a wheel with blades or vanes attached to it. When the exhaust gases from the engine pass through the turbine side of the turbocharger, they drive a shaft connected to the turbine wheel. This shaft is connected to the compressor wheel on the other side of the turbocharger through a central shaft known as the turbocharger shaft.
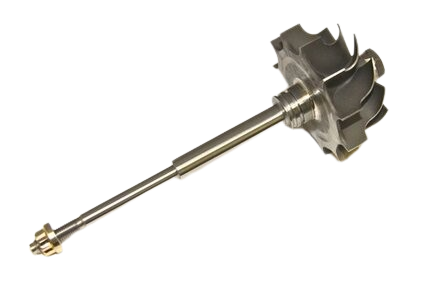
Turbocharger shaft wheels can be made from nickel-based alloys in certain applications. Nickel-based alloys, such as Inconel and Mar-M, are known for their exceptional high-temperature strength, corrosion resistance, and resistance to thermal fatigue. These properties make them suitable for use in components subjected to extreme operating conditions, such as turbocharger shaft wheels.
Inconel, for example, is a family of nickel-chromium-based superalloys that offer excellent mechanical properties at high temperatures, making them ideal for use in turbine engine components, including turbocharger shaft wheels. Mar-M alloys, another type of nickel-based superalloy, are specifically designed for high-temperature applications and are commonly used in turbocharger turbines and other aerospace and automotive components.
Nickel-based alloys provide turbocharger manufacturers with the ability to design shaft wheels that can withstand the demanding conditions of turbocharger operation, including high rotational speeds and elevated exhaust gas temperatures. Additionally, these alloys offer good resistance to oxidation, corrosion, and creep, which further contribute to the durability and longevity of turbocharger components.
Advantage of Turbocharger Shaft Wheel
- Increased Engine Power: One of the primary advantages of a turbocharger shaft wheel is its ability to increase the power output of an engine without increasing its displacement. By compressing the intake air before it enters the engine cylinders, the turbocharger allows more air (and therefore more oxygen) to be supplied to the combustion process, resulting in improved combustion efficiency and increased engine power output.
- Improved Engine Efficiency: Turbochargers help improve engine efficiency by allowing the engine to extract more power from the same amount of fuel. This is achieved by increasing the air-fuel mixture density through compression, which leads to more efficient combustion.
- Enhanced Torque Characteristics: Turbochargers can significantly improve an engine’s torque characteristics, especially at lower engine speeds. This is particularly beneficial for vehicles where low-end torque is important, such as in heavy-duty trucks and performance cars.
- Downsizing and Fuel Efficiency: Turbocharging enables engine downsizing, where a smaller displacement engine can replace a larger one without sacrificing power. This downsizing, coupled with turbocharging, contributes to improved fuel efficiency by reducing engine weight and internal friction while maintaining or even enhancing performance.
- Environmental Benefits: By improving engine efficiency and reducing fuel consumption, turbochargers contribute to lower emissions of greenhouse gases and pollutants, such as carbon dioxide (CO2) and nitrogen oxides (NOx). This aligns with the global efforts to reduce the environmental impact of automotive transportation.
Material Information of Turbocharger Shaft Wheel
- Inconel Alloys: Inconel is a family of nickel-chromium-based superalloys known for their exceptional high-temperature strength, corrosion resistance, and resistance to thermal fatigue. These properties make Inconel alloys well-suited for use in turbocharger components, including shaft wheels. Common grades of Inconel used in turbocharger applications include Inconel 718 and Inconel 625.
- High-Temperature Strength: Nickel-based alloys like Inconel offer high tensile and yield strength even at elevated temperatures, which is crucial for withstanding the mechanical stresses experienced by turbocharger shaft wheels during operation.
- Corrosion Resistance: Inconel alloys exhibit excellent resistance to corrosion and oxidation, making them suitable for use in environments where exposure to high temperatures and corrosive exhaust gases is common.
- Thermal Fatigue Resistance: Turbocharger shaft wheels made from Inconel alloys are designed to withstand repeated cycles of heating and cooling without experiencing significant material degradation or fatigue, ensuring long-term durability and reliability.
- Manufacturability: While nickel-based alloys like Inconel offer superior performance characteristics, they can be more challenging to machine compared to other materials such as aluminum alloys. Specialized machining techniques and tools may be required to manufacture complex turbocharger shaft wheel designs from nickel-based alloys.
- Weight Considerations: While nickel-based alloys provide excellent mechanical properties, they are typically denser than lightweight materials like aluminum and titanium alloys. This may impact the overall weight of the turbocharger assembly, although the specific design and application requirements will determine the significance of this factor.
Sources
- American Foundry Society. “Metal Casting”
- Wikipedia. “Investment Casting“, “Sand Casting“
- efunda. “Sand Casting“
- The Investment Casting Institute. “What is Investment Casting?“
- The Library of Manufacturing. “Investment Casting“
- Forging Industry Association “Forging Industry“
Our Internal Resources for Die Casting, Investment casting, Forging and Sand Casting
- Die Casting
- Aluminum Die Casting
- Zinc Die Casting
- A356 Aluminum Casting with T6 Heat Treatment
- Magnesium Die Casting
- Investment Casting
- Stainless Steel Casting
- Duplex Stainless Steel Casting
- Super Duplex Stainless Steel Casting
- Titanium Casting
- Carbon & Low Alloy Casting
- Forging
- Cold Forging
- Hot Forging
- ECO BRASS C69300 Brass Forging
- Sand Casting (Aluminum Sand Casting, Ductile Iron Sand Casting, Gray Iron Sand Casting)
- Specialty Fittings and Fasteners
- Precision CNC Machining and Secondary Operations